Eco-Friendly Polymer-Based Thin Film For Printed Electronics
The polymer thin film is also robust to high temperatures and highly flexible, making it great for developing electronics that are light and have a very little negative impact on the environment.
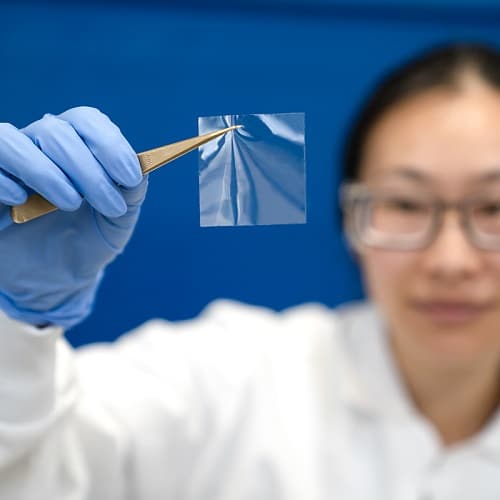
Manufacturing of electronic products and their improper disposal is often counted as one of the reasons for environmental damage. Despite deriving several key elements such as lead, nickel, arsenic, barium and many more from nature, prolonged exposure to such heavy metals is known to cause severe health issues and atmospheric deterioration. And at the same time, electronics are indispensable for spearheading the technological revolution. It’s an ongoing dilemma.
To tackle this problem, manufacturers are gradually promoting green electronics, which consists of identifying and incorporating biodegradable elements into electronic products. Although it is an emerging field and not yet fully established, it does have the potential to improve the situation.
A byproduct of that green electronics research is the Hyaline, a thin polymer film made for electronics. It is developed by Zymergen, an organisation working on building nature and biology-inspired electronic products.
“The problem for a lot of potential products that came along had been in scale-up and optimisation was something the industry needed. We think that biology opens the world, we wanted to bring impossible materials to market and we thought we could build a technology that no one else has,” said Josh Hoffman, CEO and co-founder, Zymergen.
Exceptional features
Just as conventional electronic components are made using complex chemical procedures, the thin-film is made of a polymer known as polyamide using the process of fermentation, the very same process that is involved in brewing beverages, baking bread and preparing yoghurt.
While the process might seem to be a bit odd and the end product even odder, it does have its benefits. Hyaline has high-temperature resistance and excellent mechanical properties, perfect for creating flexible printed circuit boards (PCBs) that are 30 per cent thinner as compared to traditional PCBs that contain epoxy/acrylic adhesive layers.
Using Hyaline, printed electronics (like PCBs) can be manufactured through standard reflow soldering. Coupled with the thin-films high-temperature resistivity, a faster processing time during manufacturing can be achieved.
And it doesn’t end there…..
Hyaline has high-optical clarity and very-low birefringence (a refractive index that depends on the polarization and propagation direction of light). This allows usage in touch sensor panels, as well as printed electronics and high-frequency substrates.
Light-weight applicability
Packed with such amazing features, Hyaline can be used for producing flexible that can, in turn, be used for creating foldable and portable electronic products that are much robust to physical impacts. Since it is also eco-friendly and made entirely out of the natural process, it poses less risk to the environment.
It will take time for the concept of green electronics to firmly establish itself amongst electronics industries and users, but this initiative is a good sign that integrated chips and other semiconductor devices will become even more compact and less rigid while retaining their electrical properties.
~~~~~~~~~~~~~~~~~~~~~~~~~~~~~~~~~~~~~~~~~~~~~~~~~~~~~~~~~~~~~~~~
please keep in touch by subscribing to my blog and please write to me at the comment section down below...i would be happy to have constructive criticisms from my viewers....!!!
Comments
Post a Comment
Hey..!!
Nice to meet you...
Stay connected :D